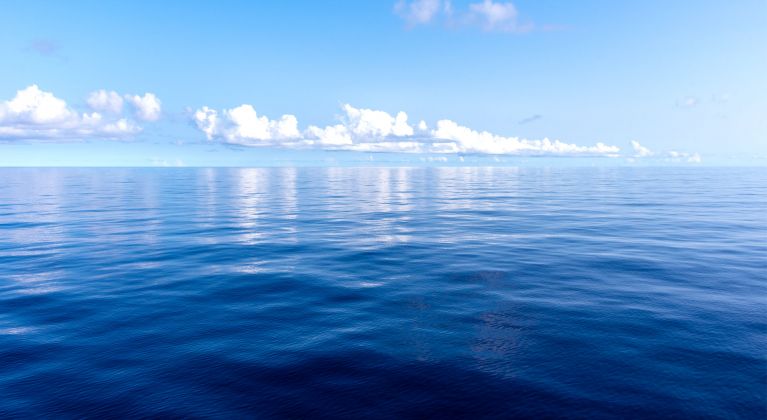
Methods of compliance with the 2020 Sulphur Limit
- Home
- Latest updates
- News
- Methods of compliance with the 2020 Sulphur Limit
Last year, the Club produced an infographic which provided preliminary information on the 2020 Global Sulphur Limit. As the deadline to comply draws closer, we would like to provide further guidance, on the methods that Members may adopt to comply with the impending regulatory changes.
In our earlier publication we identified four possible methods that Members could opt for, in order to comply with the sulphur cap of 0.5% m/m:
- Install a scrubber system which will allow vessels to use whatever fuel oil is available.
- Switch to low sulphur oil, for example Intermediate Fuel Oil (IFO) or Heavy Fuel Oil (HFO) that has been treated to reduce the sulphur content.
- Switch to a distillate fuel such as Marine Diesel Oil (MDO) or Marine Gas Oil (MGO).
- Use an alternative fuel source like Liquefied Natural Gas (LNG), Liquid Petroleum Gas (LPG), Methanol or Hydrogen.
Read more about these methods in the tabs below.
Scrubber systems vary between manufacturers but the predominant types are ‘open’ and ‘closed’ loop systems.
The open loop scrubber is associated with the discharging of flushing water containing sulphur and sulphuric acid over board. These types of scrubbers have the biggest impact on the marine environment the use of which have already been banned in many ports for fear of their impact on the local marine environment. Consequently, more ports may enforce restrictions and scrutiny in respect of open loop scrubber systems.
The closed loop scrubber is continuously re-circulating and treating the flushing water on board, therefore its environmental impact is lower than open loop systems. However, this system will produce a significant amount of residue and sludge containing sulphur, carbon and caustic. Disposal of this sludge will be problematic economically and will require additional logistical management.
The advantage to fitting a scrubber system is that the ship will be able to continue to use existing fuels. However due to the technical installation and financial implications, this option may be more attractive to Members with new build projects or that have recently built a suitable vessel approaching its first docking survey.
Switching to a low sulphur fuel oil may be a convenient option for vessels that trade in areas where this will be permitted and that do not have the space to retrofit a scrubber system or do not deem it necessary, or viable to procure distillate fuel, which is more expensive. It may be beneficial to plan for the procurement of fuel oil in advance, sourcing reliable suppliers in the vessels usual trading areas. Signing long terms agreements and purchasing bunkers in advance helps to guarantee the quality of the supplied bunkers and provide the option of immediate replacement in the event that fuel is found to be off spec.
The switch to distillate fuels was proven feasible with the implementation of the Emission Control Areas (ECAs) on 1st January 2015. Here a more stringent sulphur content cap in emissions of 0.1% m/m was achieved without major interruptions in the supply and demand of fuel. There are of course the financial implications to consider as MDO and MGO is more expensive than heavy fuel oil (HFO) used with scrubber systems and low sulphur oils. Exclusive use of distillate fuel allows for ease of movement in and out of ECAs, however detailed records should be maintained if a vessel is switching between fuel types when transiting back and forth within a controlled area.
Whilst alternative sources of fuel are mostly still in the research and development stages, some Members may have already invested in, or are exploring the incorporation or retrofitting of alternative fuel systems on board their vessel(s). This option also takes into account any possible future changes to MARPOL regulations with the introduction of the initial greenhouse gas strategy, which further aims to reduce the collective impact on the environment.
Changeover between fuel sources and record keeping
It is important that a system is put in place to record the details of any changeover between fuel oil types, installation of any scrubber system and any associated maintenance records. It should be clear to any person viewing vessel records that the sulphur cap requirements have been complied with, this is necessary in order to avoid any potential fines which may be imposed by Port State Control following inspections. Where there is utilisation of different fuel types, segregation should be maintained and tank cleaning records and fuel test results should be made available on board.
Crew training and familiarisation
Where implementation of a new system or process is introduced on board, it is important to consider that crew may not have prior experience of the operation of such systems. Any possible training needs should be identified in accordance with Member’s own professional development structures. Existing procedures, checklists and risk assessments may also require revision to incorporate any changes.
Conclusion
It is envisioned that operators of larger vessels may be more likely to adopt scrubber systems, as they require space for installation, which may not be available on smaller tonnage. Availability of dry dock spaces for retrofitting on existing vessels may also restrict operators from choosing this option. Switching to low sulphur oil (treated IFO or HFO) may then be the next financially viable option if scrubber systems are not possible. Members who are able to, may opt to switch to distillate fuels that are more expensive but have naturally lower sulphur contents, especially where their vessels are intermittently trading within an ECA. Some Members may of course choose to invest in technological developments, selecting alternative fuels. Whilst this may have a relatively slow uptake in its infancy, as further technical advances are developed more vessels are expected to be fitted with these new systems.
Accurate and clear records are vital to demonstrate the vessel’s compliance with the revised sulphur limit. Members are encouraged to ensure their systems are robust enough to avoid doubt.
The implementation date for the new Sulphur 2020 emission regulation is rapidly approaching. This is a crucial time for Members to finalise their decision as to which option(s) best suits the vessels under their management, in order for continuing compliance with this new environmental regulation.
If any assistance is required on the subject, please contact the Loss Prevention Department.