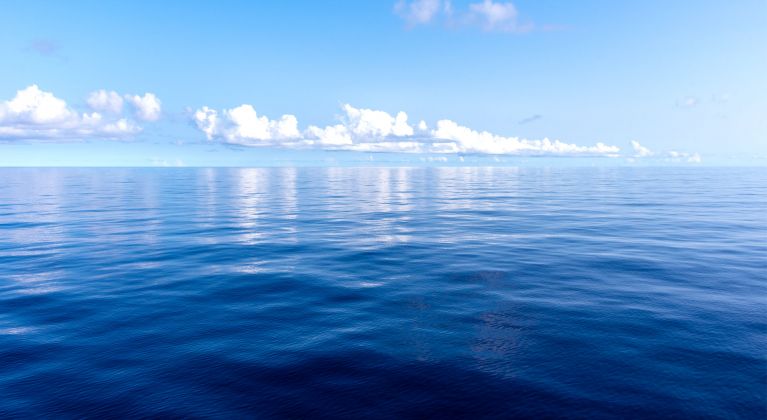
AqualisBraemar Technical Services Ltd: Floating docks and their operating hazards
- Home
- Latest updates
- News
- AqualisBraemar Technical Services Ltd: Floating docks and their operating hazards
AqualisBraemar is a leading provider of Hull & Machinery damage surveys, P&I surveys, risk assessments, inspections and audits providing 24/7 worldwide emergency response. M.K Cheah joined AqualisBraemar in 2009 as a naval architect for the Asia Pacific region. His experience is in shipbuilding, offshore construction and shipyard operations. M.K conducts shipyard risk assessments, warranty surveys for various types of heavy lift projects, towage, H&M and casualty.
A floating dock (FD) is often seen as a viable option for the dry docking of smaller vessels which alleviates the necessity to utilise a fixed land-based graving dock. However it must be borne in mind that the risks involved with operating a floating dock are substantially more than those associated with a graving dock.
Hazards
Although an FD remains stationary for most of its operational life, there are significant risks involved in certain specific circumstances:
1. Geographical
The roadmap to safe operations of the floating dock begins all the way from the planning stage wherein a suitable location is selected. Geographical location of a shipyard will determine the selection of a floating dock. These factors would ideally include water depth, proximity of the FD to adjacent shipyards, local marine traffic and weather conditions such as exposure to typhoons, seismic activities and tsunamis.
On two separate occasions, FDs located in South East Asia suffered damage to their side shell plates, securing piles and ramps due to waves generated from a third-party vessel. The first case involved a vessel that was returning from a sea trial and was travelling at an excessive speed while passing near an FD which was moored at a nearby shipyard. The wake generated from the passing vessel washed over the FD, causing it to roll significantly and damage was sustained to the piles.
The second case involved a jack-up barge that was being launched from a shipyard seafront. An FD was located across the basin on the opposite bank. During the launching of the jack-up barge, large waves were generated which swept across the basin and washed onto the FD thereby damaging its side shell plates and piles.
Shipyards in busy shipping hubs such as Singapore are generally located close to one another and the hazards from passing vessels and ship-launching operation cannot be ignored. Similarly, FD’s located in areas prone to tsunamis may place them at a higher risk. Even if there are early tsunamic warnings, relocating an FD takes several hours. Firstly, the FD must be freed from any load, the locking system and ramps have to be removed, the cranes on the exposed FD have to be stowed and tugs with correct towing gear need to be available to commence the move.
For shipyards located on riverbanks or in shallow waters, the FD must be regularly towed to deeper water for the docking operation where there is an increased risk of encountering adverse currents, collision with other vessels and risk of grounding during the move.
2. Operational
The most critical stage in the operation of an FD is when the floating dock commences de-ballasting in order to lift the vessel out of the water for docking. The weight of the vessel and the location of its centre of gravity (CG) must be accurately accounted for. Any wrong information or estimation of weight and its corresponding CG may lead to excessive trim and/or list – in serious cases the loss of positive stability results in the sinking of the FD and the docking vessel. It is paramount to monitor the stability of the FD during the docking stage.
A submerged FD has marginal reserve buoyancy and with the relatively small waterplane area from the wing walls, the FD is sensitive to any unplanned weight shifts or incorrect sequence of ballasting. Malfunctioning of remotely operated valves or ballast pumps can lead to uneven ballasting conditions, excessive trimming or stressing of the FD and may have a detrimental impact on the FD, in some cases rapid and excessive trimming and listing leads to a loss of buoyancy and sinking.
In one case, an FD sank when it was trimmed excessively during a docking operation due to the failure of ballast valves. This excessive trim resulted in the aft vent pipe openings being submerged underwater, leading to rapid flooding of the compartments and the FD subsequently sank at the berth.
In another case, an FD sank due to inaccurate positioning of the keel blocks. Several keel blocks punctured the pontoon deck when the FD was emerging from the water, causing flooding to many of the ballast tanks which led to a rapid loss of buoyancy and its eventual sinking.
The cranes on board the FD are positioned high on the side wall top deck and they are subjected to strong winds thereby making them vulnerable to the risk of toppling over during bad weather or squalls. In the region of Sumatra, Malaysia and Singapore there is a weather phenomenon called Sumatran Squalls that normally develops early in the morning between 0200hrs and 0500hrs whereby winds gust up to 50 knots. When faced with the squalls, FDs can be exposed to situations such as toppling cranes or parting of mooring lines. FDs should ensure that all cranes are stowed properly with their crane booms rested in their home position whenever not in use. Having a night watch keeper on deck to monitor the FD’s mooring lines will also go great lengths to ensure the safety of the FD. Members can also consider installing CCTV to keep a visual check along with live weather feedback to monitor the situation.
3. Maintenance
FD pontoon decks are subject to numerous mechanical abrasions, heat damage from welding and general wear and tear, causing the protective coating to lose effectiveness. This can then expose the steel to the elements, accelerating its corrosion and results in the diminution of the steel thickness. Over time, the strength of an FD is reduced and any error in ballasting or loading may result in damage to the FD or even a total loss.
Members must ensure that a robust planned maintenance programme of the FD is in place and should be strictly adhered to even if the FD may have a tight docking schedule to meet. Periodic steel thickness gauging on critical structural members must be carried out. It is also necessary that a regular maintenance of the paint work to arrest any corrosion be included in the planned maintenance programme. There have been instances where poor structural condition has compromised the watertight integrity of FDs causing them to sink. A strict servicing/maintenance programme for ballast valves, pumps, motors and vents is essential. This maintenance plan must include periodic inspection, testing and overhauling of the ballast valves including remote monitoring and level alarm systems of the ballast spaces. In some cases, ballast migrating into non-designated tanks by way of faulty ballast valves, which may not have been detected due to the malfunctioning of the detection systems, has caused the FD to sink or flounder.
Conclusion
FDs can be prone to significant hazards and therefore are required to be operated with great care by experienced and knowledgeable personnel including strict adherence to procedures and adequate training for the docking master and the rigging crew.